Why integrate remote visual inspection
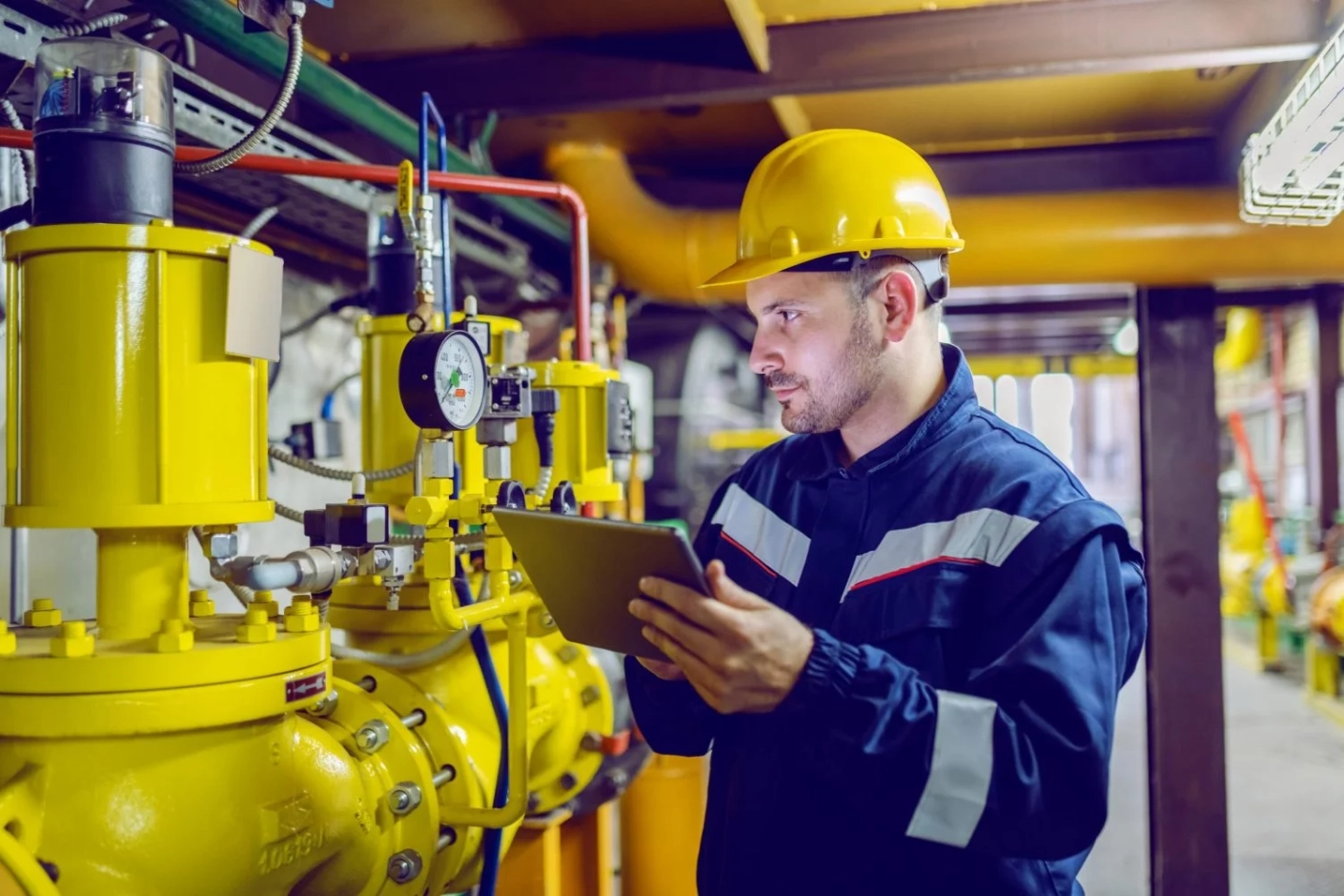
Distance became the new normal in many areas during the COVID-19 pandemic. Digital technologies have made it possible to collaborate from thousands of miles away and ensure continuity of production and services. These innovative remote technologies have been used in inspection activities in various sectors. Whether for risk and asset management, industrial maintenance, site or supply chain inspection, remote visual inspection has proven its value over the long term. It increases efficiency, reduces costs and improves safety.
Why implement remote visual inspection
Inspection activities are common in various sectors. They typically involve testing and measuring equipment or a site. The results are compared to specific standards and requirements to determine if the equipment or site is in compliance with set objectives.
Traditionally, inspections have taken place onsite, but more and more companies are adopting digital tools and technologies in inspection operations to the point that according to a recent ReportLinker study,the global digital inspection market is expected to reach $28.9 billion by 2025. The adoption of digital solutions can optimize inspections and generate time and cost savings.
Remote visual inspection solutions are part of these inspection digitalization solutions. Remote visual inspection is a process that allows an expert to inspect a piece of equipment or a site remotely through equipment such as smartphones, tablets, connected glasses and headsets, remote cameras, drones or endoscopes. This process allows the quality and integrity of equipment and assets to be verified according to company and industry standards, without having to travel. Remote visual inspection allows people to collaborate from thousands of miles away or in hard-to-reach areas or equipment, in various industries such as manufacturing, automotive, aerospace, construction, certification, maritime, oil & gas or energy.
Remote visual inspection use cases
Remote visual inspection solutions go far beyond the simple transmission of a video stream. For example, Apizee’s remote visual inspection solution includes features such as multi-participant inspections, document sharing, remote HD photo taking, recording, real-time annotations, video pointer guidance, inspection checklists that enable a workflow of inspection points to be followed, defect recognition and characterization, electronic signature and automatic generation of inspection reports.
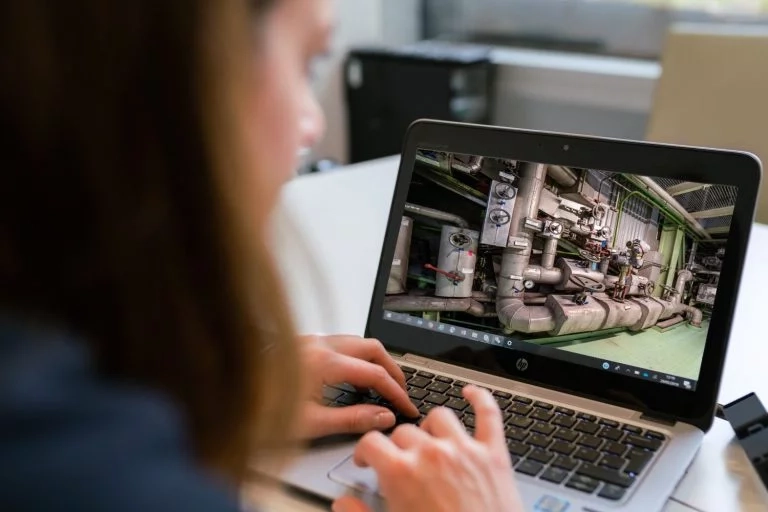
Remote visual inspection can be used for various purposes:
- Risk and asset management: risk management consists of identifying and evaluating the threats to which a company is exposed. In this context, remote visual inspection can be used to conduct virtual audits, inspect and certify specific components during manufacturing or commissioning, or reduce the risk to personnel when inspecting hazardous equipment. With remote inspections, companies can ensure business continuity while maintaining both the safety and compliance of their assets and products. Remote inspections also enable faster decision making and response times. This use case can affect companies in the oil & gas, maritime, offshore, automotive, construction, pharmaceutical, energy and other sectors.
- Industrial maintenance: downtime and unexpected machine breakdowns are events that can have significant impacts in terms of costs and organization in a production line. Remote visual inspection can help reduce machine downtime. It can reduce the risk of breakdowns by making preventive inspections more reliable thanks to the remote presence of an expert who supports the technician during the inspection. It can also play a role when a failure happens. When a breakdown occurs, a race against time begins and it can take several days for a properly trained technician to arrive on site. A remote expert can quickly assist a technician on site and guide him in the inspection of the machine or equipment to arrive at a faster diagnosis.
- Building and site inspections: Building and site inspections are part of the daily routine of architects and civil engineers. In addition to being essential to safety and quality management, efficient and timely inspections are a crucial factor in meeting deadlines. The complexity of some large projects requires the architect to visit the site regularly to clarify issues as they arise. A recent study shows that70% of the requests for extension of delivery deadlines are related to problems of access to the site. Often, these assessments require the presence of several contractors. Remote visual inspection allows architects, engineers and other involved parties to be brought together easily and without travel.
- Supply Chain Inspection:Inspections of suppliers throughout the supply chain provide assurance that equipment purchased will meet specifications and minimize the financial impact of defective equipment. They can range from operational risk to product verification. They can be conducted by the company itself or by specialized third-party companies. Depending on the product, confirmation of compliance may require the involvement of multiple experts. Suppliers can also be multiple and located around the world. Whether it’s an in-house or outsourced process, remote visual inspection can be useful to call upon several experts at the same time and to reduce travel to different suppliers.
Benefits of Remote Visual Inspection
The adoption of remote visual inspection accelerated due to the travel bans and distancing standards put in place during the COVID-19 epidemic. During this time, remote inspection has enabled the continuity of critical infrastructure projects and has proven its long-term value to a variety of industries. It increases efficiency, reduces costs and improves safety. Here are some of the benefits of using remote visual inspection:
- Acceleration in decision making: remote inspection reduces response times, allows multiple team members to be involved in an inspection and get their input immediately. This way, decisions can be made more quickly.
- Improved operational efficiency:Eliminating travel means more inspections can be completed in the same amount of time. The efficiency benefits are also extended to the customer by reducing the wait time for an inspector to be available.
- Improved safety: With remote visual inspection, fewer people will be required on site, reducing on-site risks.
- Reduced carbon footprint: Remote video inspections reduce travel to sites, which are often dispersed across the country and even internationally. Transportation was responsible for 34% of greenhouse gases in the UK in 2019.. Limiting these visits and conducting virtual inspections could help reduce a company’s carbon footprint.
- Ensure business continuity: Inspections can continue regardless of access to the supplier site or travel restrictions.
- Increase inspection frequencyfor customers with remote locations to mitigate risk.
- Improved employee well-being:reduced auditor and inspector fatigue due to travel.
Safran Aircraft Engines: a concrete example of the implementation of remote visual inspection
Safran Aircraft Engines designs, develops, produces and markets engines for civil and military aircraft and satellites. Safran Aircraft Engines offers B.SIde®, a remote visual inspection service dedicated to endoscopythat brings together its experts and airline technicians around the world in a single click This turnkey service helps airline technicians to speed up decision making during engine borescope inspections, in order to reduce aircraft downtime. This service saves more than €2 million in heavy operations per year.
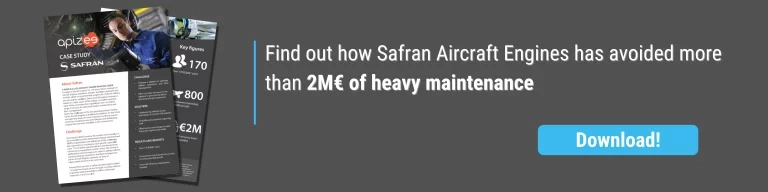
Apizee’s video-assistance solutions can fully address the needs and issues of remote visual inspection and are already being used by players in a variety of industries. Our teams are ready to assist you in the implementation of video assistance for remote visual inspection. Contact us to learn more or to get a demo.
Read also:
- With Apizee Diag, Safran Aircraft Engines has helped to save millions to its customers
- How to reduce downtime on a production site thanks to visual assistance
- Visual assistance to meet the operational challenges of the offshore oil and gas industry