How to reduce downtime on a production site thanks
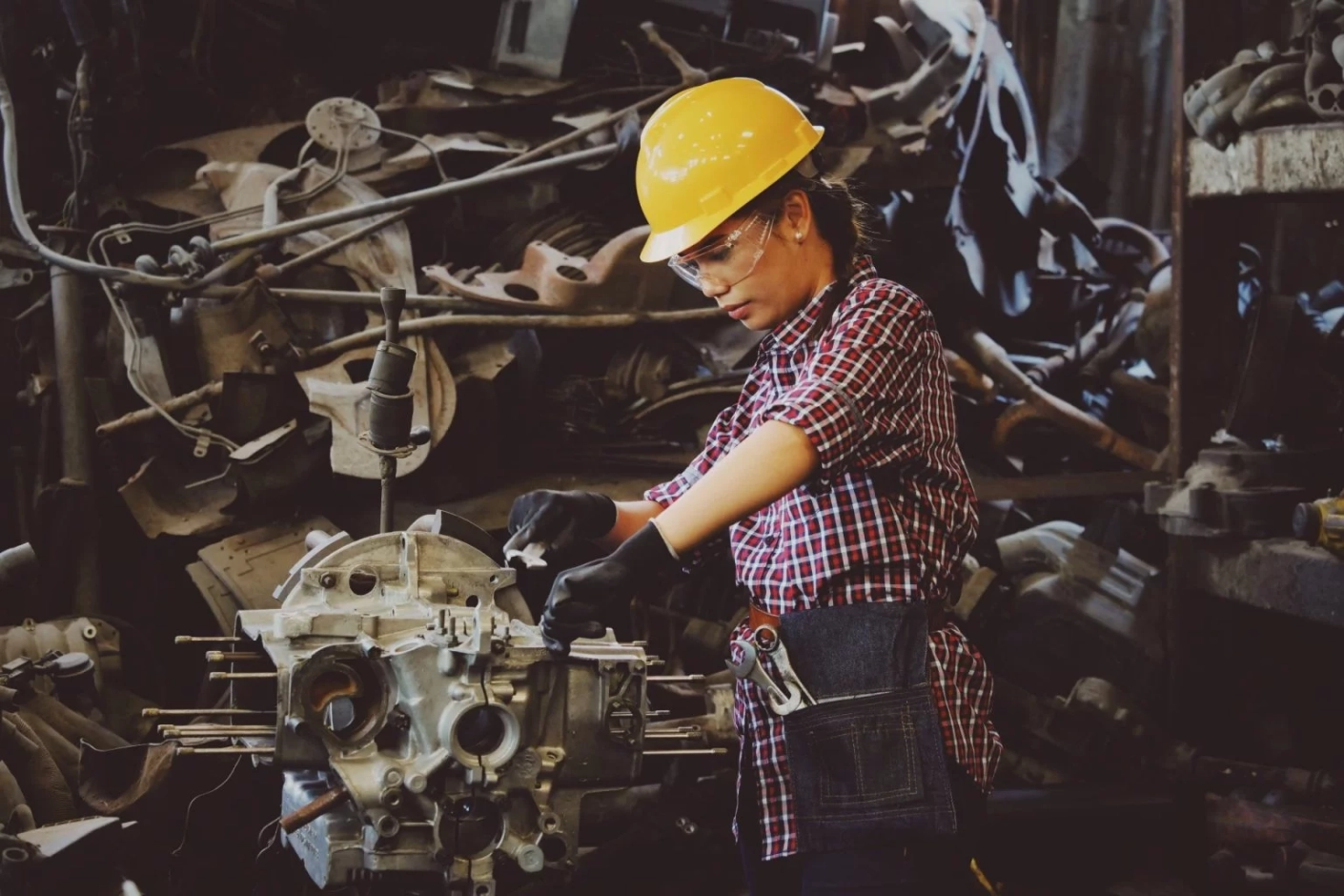
Unplanned machine downtime and breakdowns in the industrial sector are events that can have significant impacts in terms of costs and organization in a production line. According to a study by Aberdeen Research, the cost of downtime in the industry has increased significantly. At the end of 2016, 82% of companies surveyed had experienced unplanned outages in the past three years, which represents a cost of up to $260,000 per hour. Reducing machine downtime is a key issue in the industrial sector and the coupling of visual assistance with predictive maintenance solutions can help to achieve this goal.
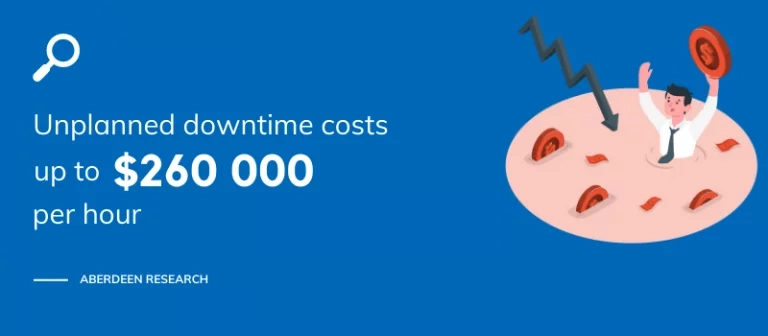
How to define downtime in the manufacturing industry?
Downtime is defined as the period of time during which a machine is unavailable. Total machine downtime means lost production for the company.
Two types of downtime can be distinguished:
- Planned downtime: this is scheduled and budgeted production downtime, such as maintenance, cleaning, scheduled adjustments or replacement. Even when planned, downtime always have a cost, so the priority is to respect the deadlines set for the operation and to be able to anticipate and act in case of unexpected events.
- Unplanned downtime: this is downtime that occurs as a result of an unexpected event such as an equipment failure. The time required to remedy the failure is often dependent on the availability of parts to repair the equipment, as well as the availability of a skilled workforce capable of diagnosing and resolving the problem.
Possible causes of unplanned downtime
Recently, Vanson Bourne conducted a study for Service Max, “After The Fall: Cost, Causes and Consequences of Unplanned Downtime” with 450 industrial services and IT decision makers in the U.K., U.S., France and Germany, including manufacturing, medical, oil and gas, energy and utilities, telecommunications, distribution, logistics and transportation. This study focuses on the causes and impacts of unplanned downtime in companies.
The study highlights two main causes of unplanned downtime:
- According to the study, human error is one of the leading causes of downtime in the industry (23%), which is not surprising considering the range of increasingly hyperspecialized machines and equipment that require the maintenance and intervention of maintenance technicians and engineers
- The second cause that emerges from this study is the lack of knowledge of equipment condition. In fact, 70% of companies surveyed do not know the exact condition of their equipment or when it needs to be maintained, upgraded or replaced.
What are the real costs of downtime?
True Downtime Cost (also known as TDC) is the analysis of all cost factors associated with downtime.
There are two types of costs, tangible and intangible.
Tangible costs are the physical consequences of downtime in manufacturing and are usually easily quantifiable:
- Loss of production: each product represents a certain amount of potential profit, each unit that stops being produced during the downtime represents a loss of profit.
- Labor costs: when equipment breaks down, the company produces less, even though it continues to use the same amount of labor. Sometimes these costs can even increase if the maintenance crew has to work overtime to make the repairs.
- Loss of stock: in factories working with perishable goods, production downtime can result in the loss of expired batches.
In addition to these tangible costs, there are intangible costs that are less obvious to quantify. Many of these costs are related to the way humans and machines interact:
- Responsiveness: When downtime occurs, employees must make resolving these issues their top priority and are less available to handle other critical tasks.
- Stress: downtime is a source of stress for all teams.
- Loss of customers: if the factory is not able to compensate for lost productivity and customers are not delivered on time, they may question your ability to deliver products on time and look to work with more reliable suppliers.
- Innovation: downtime is an obstacle to creativity. When the company’s attention and resources are all devoted to fixing equipment and solving production problems, there is no energy or capital left for innovation. In the long run, this cost can greatly restrict a company’s competitiveness.
How does video assistance help reduce unplanned downtime?
For years, predictive maintenance has been one of the essential tools for reducing production downtime in the industrial sector. It allows to know better the state of an equipment and to foresee the breakdowns before they occur. Although it is currently very popular, it is not an entirely new concept. Without really using this term, industrial players have been doing predictive maintenance for many years. When a technician performs a visual inspection and chooses – based on knowledge, experience and intuition – the best time to shut down a piece of equipment in order to repair it, he or she is in fact performing predictive maintenance.
According to a PWC survey on predictive maintenance with maintenance managers in a wide range of industries and company sizes, 27% of the companies surveyed use visual inspection as their primary method of predictive maintenance and 36% of them combine the technician’s expertise in visual inspection with instrument readings.
The visual approach still has an essential role in predictive maintenance and visual assistance can greatly contribute to optimizing and making visual inspections more reliable.
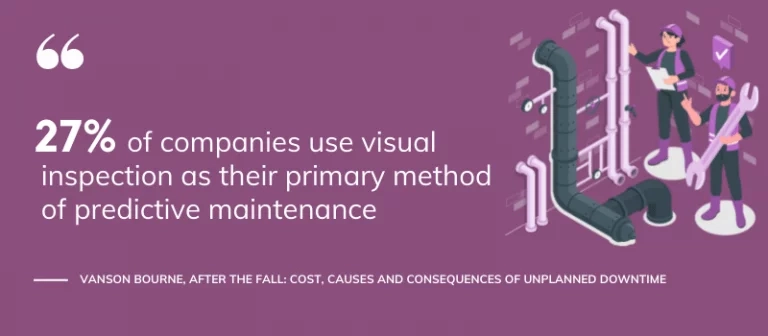
Visual assistance to make visual inspections more reliable
Human error, often due to inadequate training or fatigue, can lead to inaccurate and inconsistent conclusions. For example, visual assistance allows a technician to be supported remotely during a visual inspection, which leaves less room for error. The remote expert can confirm the correct operation of the machine and answer questions. The recording and photo-taking features also allow you to keep track of each inspection.
Fault detection integrated in visual assistance solutions
Thanks to the integration of Artificial Intelligence capabilities in visual assistance solutions it is now possible to carry out inspections at critical points in a production line, even in hard-to-reach areas, and to automatically recognize and characterize defects that could go unnoticed on a simple visual inspection.
Visual assistance to manage unexpected downtime more quickly
When an equipment shutdown occurs, a race against time starts to get it back up and running as quickly as possible. But with highly specialized machines, it can take several days for a properly trained technician to arrive on site. That’s when visual assistance comes into play. A remote expert can quickly assist an on-site technician and guide them through diagnosis and troubleshooting using video communication enhanced with augmented reality and collaboration tools.
Visual assistance is therefore a very interesting tool to integrate into your predictive maintenance approach for the reduction of unexpected downtime. Whether as a basic tool or coupled with real-time monitoring and Big Data tools, it can play a key role in improving equipment condition awareness as well as reducing human error. Please contact us if you would like to learn more about Apizee’s visual assistance solutions and how they can be integrated into your predictive maintenance processes.
Discover our visual assistance solutions Contact us for a demo
Read also:
- 10 reasons to use real-time video assistance in the industry
- 8 key factors to consider when choosing a remote visual assistance solution for your technicians
- With Apizee Diag, Safran Aircraft Engines has helped to save millions to its customers